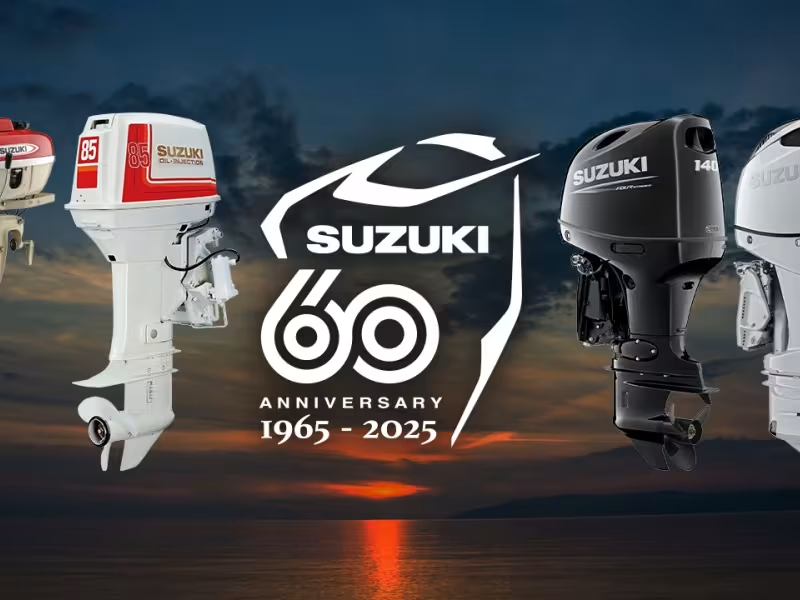
SHERIDAN, WYOMING – April 20, 2025 - A new anodizing process enhances durability, supports complex designs, and cuts CO₂ emissions in half
Innovative Technology Enhances Motor Durability
New treatment boosts resilience of engine components
Suzuki Motor Corporation has announced a major advancement in corrosion protection for its outboard motors. A newly developed anodizing process now strengthens key engine parts that must endure extreme heat, including the cylinder head and crankcase. This innovation has been integrated into the production of the DF140B model since August 2024 and will gradually expand across the product line.
Uniform Coating Improves Water Resistance
Cooling system components receive optimized protection
Because outboard motors operate by circulating large volumes of water for cooling, corrosion protection within the cooling water channels is vital. Suzuki’s new technology ensures even coating of these parts, significantly enhancing their resistance to water damage. Additionally, this process helps cut CO₂ emissions by approximately 50% compared to traditional surface treatment methods.
Advanced Anodizing for Complex Shapes
Aluminum parts gain a robust oxide layer
The new anodizing technique involves immersing aluminum components in an electrolytic solution and applying an electric current to form a tough aluminum oxide layer. This layer increases corrosion resistance while a novel immersion method eliminates air pockets, enabling consistent treatment even on intricate cooling channel geometries.
Heat Resistance Achieved Through Low-Temperature Sealing
Coating integrity maintained at high operating temperatures
To combat potential cracking of the coating under high heat, Suzuki has introduced a low-temperature sealing process using metal hydrates. This technique seals microscopic pores in the surface, maintaining coating durability at temperatures up to 300°C—a first in mass production for outboard motor components.
Cylinder Liner Protection Secured with New Seal Technology
Patent-pending solution guards against pitting
Since the engine block's integrated cast iron cylinder liner is vulnerable to pitting when exposed to electrolytic solution, Suzuki has developed a special sealing mechanism to prevent contact. This innovative approach is now patent-pending.
Significant CO₂ Reduction Supports Sustainability Goals
New process eliminates need for energy-intensive steps
Unlike conventional methods requiring chemical treatment followed by painting, Suzuki’s anodizing solution streamlines the process. By removing the need for drying and baking paint, overall CO₂ emissions are reduced by about 50%.
“The new technology increases product quality and is an important step toward carbon neutrality,” said Shuichi Mishima, Executive General Manager Marine Operations at Suzuki Motor Corporation. “It’s a world-first in the mass production of outboard motors. As a company, we remain committed to advancing our outboard motor technology and delivering products that excite our customers.”
For more information, visit Suzuki Marine's official website.